The Steel Making Process
The steel making process is very complex and detailed. At the Sydney Steel Plant, as with other plants, the process was slightly different. Explore the stages and essential aspects of the steel production process.
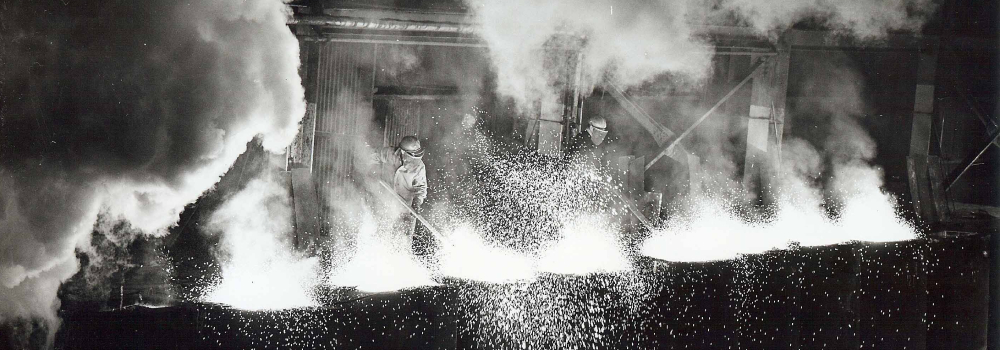
The making, shaping, and treatment of steel is a very complex procedure.
The three basic raw materials in steelmaking are:
- Iron Ore
- Limestone
- Coal
The coal is first converted to coke, by heating (baking) it in a coke oven. This coke is then used in the blast furnace procedure. The purpose of the blast furnace is to reduce the iron ore to the free metal (pig iron), and to remove the gangue (impurities) in the form of slag. The iron is then modified further by the removal of certain impurities to form steel. The addition of other elements in the process produces alloy steel.
Steel is made by various processes. The modern methods are:
- Bessemer Process
- Basic Oxygen Furnace
- Open Hearth Furnace
- Electric Arc Furnace
This steel is then taken to the rolling mills where it is rolled into numerous finished products, such as slabs, rails, or roundbars. This section of the website will examine the entire steelmaking process from raw materials to finished products.
One of the requirements for reducing iron ore into molten iron in a steel plant is coke, which is a non-volatile residue resulting from the destructive distillation of coals. Destructive distillation is the process of decomposing a substance (wood or coal) by heating it in the absence of air. Air is kept out of the oven so that the wood or coal will not fire. Coke, along with many useful volatile by-products, is produced when carefully selected bituminous coals are heated in a closed atmosphere. Coke used in a blast furnace must have the following characteristics:
- It must have enough strength to resist shattering by handling or crushing under the load of the blast furnace charge.
- It must be free of dust and particles under 3/4 inches in diameter for speed of combustion.
- It must contain as little sulphur and ash as possible as determined by the coals used in its manufacture.
Coke is a hard, greyish substance obtained when soft coal (bituminous) is heated in an airtight oven. Coke contains 87 to 89 per/cent carbon, is hard and porous, produces intense, smokeless heat when it burns and is valuable in smelting (melting) iron ore. Coke used in smelting is called metallurgical coke.
Coke was first produced in beehive ovens but is now produced in the more efficient by-product ovens. The advantages gained in these by-product ovens are; increased coke yield, through exclusion of air; shorter coking period through the narrower chambers in use and the more efficient means of utilising gases; saving in the heat of the oven through external quenching; saving of time and labour through the use of mechanical equipment.
CHARCOAL
Originally, charcoal was produced by stacking hard or soft wood in piles or long rows that were covered with earth; a small opening was left in the top through which a fire was lighted, and the wood was allowed to smolder for about 10 days. The hole was then closed, the fire smothered, and the charcoal collected. This early wood charcoal was used in the production of pig iron because of its low Sulphur content but was replaced by the more economical and efficient coke produced from bituminous coal.
Coke is the solid residue, consisting chiefly of carbon, that is left behind when bituminous coal is distilled in the absence of air. In the production of coke, a process called ” carbonization of coal ” or ” coking,” most of the volatile matter is removed by heating (baking) the coal in a closed chamber to retard or prevent burning. Nearly 90% of the coke produced from coal each year is used by the iron and steel industry for the production of pig iron.
(c.1620). A beehive oven is a simple firebrick chamber built with an arched roof so that the shape inside is that of an old-fashioned beehive. A typical oven is 12 feet in diameter and holds from 5 to 7 tons of coal in a uniform layer between 18 and 24 inches deep on the floor.
Beehive ovens were usually built in long rows, one oven beside another with a retaining wall between. Such a row of ovens is termed a ” battery”. The batteries often followed the contours of the hills in the coal fields where they were located. Railroad tracks for handling the coal to the ovens ran along the tops; and other tracks for handling the coke cars ran beside the ovens. Many beehive batteries have been located close to the mines, so that the freshly mined coal was charged directly into the ovens. No provision for stocking or mixing the coal is made at a beehive plant.
Coal is charged into an empty oven through the hole at the apex of the dome. It forms a cone-shaped pile which is levelled to a uniform layer of 18 to 24 inches by means of a rake passed through the door. The coking process is started by means of the heat retained in the walls of the oven from the previous charge of coal. New ovens are brought up to temperature by heating with coal or wood before charging.
Almost immediately after charging, gas is evolved (released) from the coal. The air for combustion is admitted through an opening at the top of the oven door. By removing or introducing bricks at the opening, the quanting of air is regulated. The coking time which depends largely on the depth of the layer of coal, ranges from 48 to 72 hours. As coking proceeds, the volume of gas evolved decreases, and the size of the opening in the door is correspondingly decreased. This prevents the entrance of an excessive volume of air, which otherwise would burn part of the coke and might be sufficient to cool the oven as well.
When coking is complete, the door is opened and the white hot charge is quenched by stream of water directed through the opening. The quenched coke is then raked from the oven by hand and loaded into train cars for transport. Beehive coking is now an obsolete process because of the small quantity it manufactured and the very large amount of pollution it produced.
By-product coking is classified as a true distillation process because all the components of the coal are recovered. One of the chief differences between by-product ovens and the beehive ovens is the source of heat. Instead of burning part of the coking coal, as in the beehive oven, the by-product oven is heated by an external fire. Several types of coking ovens are used in this process, but the basic design is similar for all types, and they differ chiefly in the method of heat application. The three best known types are the Semet-Solvay, the Otto-Hoffman, and the Koppers.
The coking chambers (ovens) into which the coal is charged are rectangular and range from 30 to 42 feet in length, from 6 to 14 feet in height, and from 12 to 22 inches in width. These chambers are constructed with silica fire-brick to withstand the extreme temperatures of the coking process. Between each oven is a series of heating flues which are arranged so as uniformly to heat the entire side of the oven.
The individual by-product coke oven operates alternately, but each oven is started and stopped at different times, so that the operation of the entire block continually produces gas of good average composition. A charge of finely crushed coal is dropped from a larry car through charging holes (usually four) in the top and into the oven, where the walls are at approximately 1100 C.
The surface of the coal in the oven is levelled and the charging holes are covered. At the top and at the ends of the coking chambers are openings for collection of the volatile matter as it evolves during the heating cycle. These openings are fitted to off-take pipes that carry the gases to chemical recovery units where the by-products of coking are obtained. The coking coal, which entered the retort (oven) as individual particles, begins to soften at about 400 C, and as the temperature rises the coal fuses into a plastic mass. Depending on the volatile matter content, the coal expands or contracts during the plastic range and gas evolution period until it resolidifies at about 500 C.
At the end of the coking cycle (approximately 17 hours), both end doors of the chamber are opened, and a “pusher” mechanism shoves the block of incandescent coke into a quenching car. The car then advances to a spray system that rapidly cools the coke to prevent combustion. After quenching, the coke is crushed and screened for proper sizing to meet specific applications.
As the name implies, the recovery of coal chemicals is an important aspect of the by-product coking process. During the cokemaking process, approximately 30% by weight of the initial coal charge is given off as mixed gases and vapours. This raw coke oven gas is drawn off from the ovens, collected and put through a refining process in the By-Product area of cokemaking. The recovery system is extremely complex, but essentially it involves the condensation or extraction of the desired products from the gases of the coke-oven exhaust stream. The gases and vapours leave the ovens at a temperature ranging from 315 to 370 C. Water sprays at strategic locations in the collecting system reduce the temperature to a range of 145 to 215 C.
The carbonization or destructive distillation of a ton (0.9 metric ton) of coal produces an average yield of about 0.7 ton (0.63 metric ton) of coke; 11,500 cubic feet (345 cubic meters) of gas; 12 gallons (45.6 Litres) of tar; 27 pounds (12 kilograms) of ammonium sulfate; 50 gallons (190 litres) of benzol; 0.9 gallon (3.4 litres) of toluol and naphtha; and 0.5 pound (0.2 kilograms) of naphthalene.
Coal tar, a thick black, sticky liquid, is the source of a great number of chemical compounds, including creosote, pitch, toluene, and naphthalene; is extracted from the stream of gases evolved during coking. Coal tar is recovered by partially condensing (changing to liquid) the hot vapours from the coke oven. This is done by means of water spray cooling towers, mechanical impingement of tar particles, and electrostatic precipitation.
Ammonia, a gaseous compound, is used in products ranging from smelling salts to agricultural fertilizers. The most common method to extract ammonia from coke-oven gas, involves the concentration of ammonia bearing vapours by use of a still and an ammonia absorber. In the absorber, the rising gases are sprayed with dilute sulphuric acid to form ammonia sulphate, which, when dried, contains about 26 5 ammonia.
Phenol (C6H5OH) is recovered from coal tar and ammonia liquor. Sometimes called carbolic acid, phenol is used in the manufacture of plastics, perfumes, picric acid, salicylic acid, cutting oils, antiseptics, and wood preservatives. The method of recovering phenol uses benzol as a solvent to remove the phenol from the ammonia liquor. Caustic soda is then used to extract the phenol from the benzol, and the final product is sodium phenolate.
Cresols (C7H8O) are used extensively in insecticides, weed killers, resins, pharmaceutical, and photographic compounds. They are in the phenol family and are extracted by a process using sulphuric acid as a converter and benzene as an extracting agent.
Toluene (C6H5OH3) is recovered both from the coke-oven gas and from the coal tar. It is used in the manufacture of chemicals, explosives, detergents, solvents, and dyes, and is also converted to benzene.
Light oil, which is one of the components of coke-oven gas contains more than a hundred compounds. The most important elements recovered from light oil are benzene, toluene, xylene, and solvent naphtha. These chemicals are then used in the preparation of solvents, plasticizers, resins, and synthetic fibres.
The coke oven gas resulting from the refinement of the raw gas is used throughout the plant as a fuel for reheating furnaces, soaking pits, coke oven batteries, boilers, and numerous other uses.
BLAST FURNACE PROCEDURE
The objectives in Blast Furnace operation are two-fold. The first objective is to reduce the iron ore to liquid metallic iron. The second is to control as far as possible the quantities of impurities which find their way into the iron either wholly or in part.
The first intentional attempt to extract iron from iron ore in a furnace-type of container was in Catalonia, Spain (circa.1300 A.D.) where a ‘Catalan’ forge (basically, a scaled-up blacksmith’s forge) was used to produce iron. The Catalan forge was anywhere from 20 inches square and 16 inches deep to around 30 inches by 40 inches square and something over 2 feet deep. The nozzle (or tuyere), through which the blast was blown into the furnace, was placed about 9 inches from the bottom in the smaller hearths and about 15 inches from the bottom in the larger hearths.
The hearth was filled to the level of the tuyere with charcoal, on which was piled lumps of iron ore mixed with charcoal. These materials were placed so as to form two separate columns, the charcoal against the tuyere side of the hearth, and the ore against the other side. A gentle blast of air was applied at first and the carbon monoxide, formed by combustion of the charcoal, passed through the open pile of iron ore. The ore was reduced to metallic iron when the oxygen in the iron oxide of the ore combined with the carbon monoxide to form carbon dioxide.
The waste gases escaped at the top of the charge. The metallic iron resulting from the reduction of the ore became pasty enough to form a coherent ‘bloom’. After as much as possible of the ore had been reduced, the bloom was pried out of the hearth and hammered into bar form. Thus began the series of developments from the small stone-built structure capable of producing 50 tons of pig iron a year to the modern 100-foot tower with a capacity of more than 2,000 tons a day.
Les Forges Saint-Maurice in Quebec was Canada’s historic first ironworks, producing castings and wrought iron bars from a charcoal-fired blast furnace in 1738. Care must be taken to distinguish between the French term ‘Les Forges’ and the English word ‘Forge’ (blacksmithing). In French historical writings, ‘Les Forges’ has a very broad meaning. It signifies a complete ironworks establishment. This included the blast furnace as well as the foundry, pattern shop and all the facilities for re-heating pig iron and hammering out wrought iron bars.
Usually the term also included the associated ore collection, charcoal burning, storehouses, workmen’s quarters, etc., i.e. the whole pioneer industrial community. All the necessary raw materials for the manufacture of iron were found in abundance within a few miles of the blast furnace at Saint-Maurice. The blast furnace at Les Forge Saint-Maurice is known to have been thirty feet in height. It can be described briefly as a cold blast, charcoal-fired furnace employing water power for the air blast and the associated forge hammer, for making wrought iron bars. The blast furnace was eventually abandoned in 1883.